押出成形とは
押出成形とは、熱可塑性の樹脂を加熱して溶かし、製品の断面形状を型どった金型に材料を押し出して加工する方法のことを指します。生クリームをパイプやチューブから絞り出すイメージをするとわかりやすいと思います。
押出成形ではチップやペレット状の材料を使用し、ホッパーを通じて加熱シリンダに投入され、ドロドロになるまで加熱されます。加熱された樹脂は、金型に押し出される形で金型の外に排出されますが、この時に金型の形状に成形されて出てくるのです。
金型で成形され押し出された樹脂は、そのままでは柔らかいので空気や水で冷却しますが、このときに形状が崩れないように「サイジングダイ」と呼ばれる金型に保持されながら、硬化されて排出されます。
硬化の方法は樹脂の種類や製品の形状によって異なりますが、薄く冷えやすい形状の場合は空冷が採用され、肉厚な製品では水冷が採用される傾向にあります。
冷却され硬化が終われば、引取機や引取ロールと呼ばれる機械に引っ張られ、その後製品の長さや定尺サイズにカットされ製品として出荷されます。
塩ビ(PVC)押出成形の特徴
塩ビは耐薬品性、耐候性、難燃性に優れた材質です。そのため、塩ビを利用した押出成形品は、屋外での使用を前提とした、断面形状が一定の長尺の製品を作るのに向いています。
最もよく目にする塩ビの押出成形品は、上下水道のパイプです。注意して見てみるとグレーのパイプが建物の周りにあるのが見えるはずです。これが塩ビ管と言われるものです。塩ビ管は耐候性や耐薬品性に優れているため、屋外であっても長期間傷むことがありません。
押出成形では形状の自由度もある程度あるため「ヨ」や「日」のような複雑な形状でも作成できるのが特徴です。この点から複雑な形状が求められる「窓サッシ」などでもよく利用されています。
従来はアルミサッシが一般的でしたが、塩ビを利用した樹脂サッシは優れた断熱性で結露を起こしにくいという理由から徐々にアルミサッシに置き換わりつつあります。
また、塩ビには軟質、硬質、発泡などのタイプがあります。塩ビであれば、いずれのタイプでも押出成形が可能です。
押出成形のメリット
押出成形のメリットには、下記の2つがあげられます。
- 断面形状が一定の長尺製品を安定して製造できる
- 射出成形に比べて金型が安価
ここまででも解説したように、押出成形では断面形状が一定の長尺製品を安定して製造できます。数メートルにも及ぶ長い棒状やパイプ状の製品は、押出成形だけが加工できるものと考えていいでしょう。
押出成形では、溶かされた樹脂が出てくる部分の金型、サイジングダイの2つを変更するだけで加工ができてしまいます。
そのため、金型部分が小さくて済むので、射出成形などに比べると圧倒的に安いコストで金型が作成可能です。
押出成形のデメリット
押出成形のデメリットには下記の2つがあげられます。
- 小ロット生産には向かない
- 寸法精度が低い
押出成形では、ある程度の材料を溶かして機械を動かす必要があるので、小ロットでの生産が難しいという点があげられます。
あまりにロット数量が少ない場合は製造を断られることも珍しくありません。また、金型を作成する必要もあるので、金型費用の面で見ても小ロット生産には向きません。
複雑な形状でも作成できる押出成形ですが、寸法精度は射出成形などに比べると低くなってしまいます。これは、溶かした状態で金型を通って製品が出てくるためです。
製品の形状にもよりますが0.1mm以下の精度を出すのは難しいです。特に中空形状などは精度が出にくいです。
押出成形に適している製品例
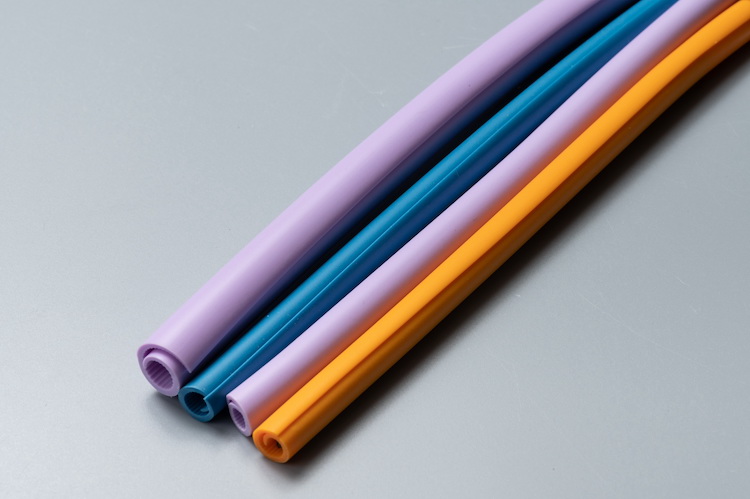
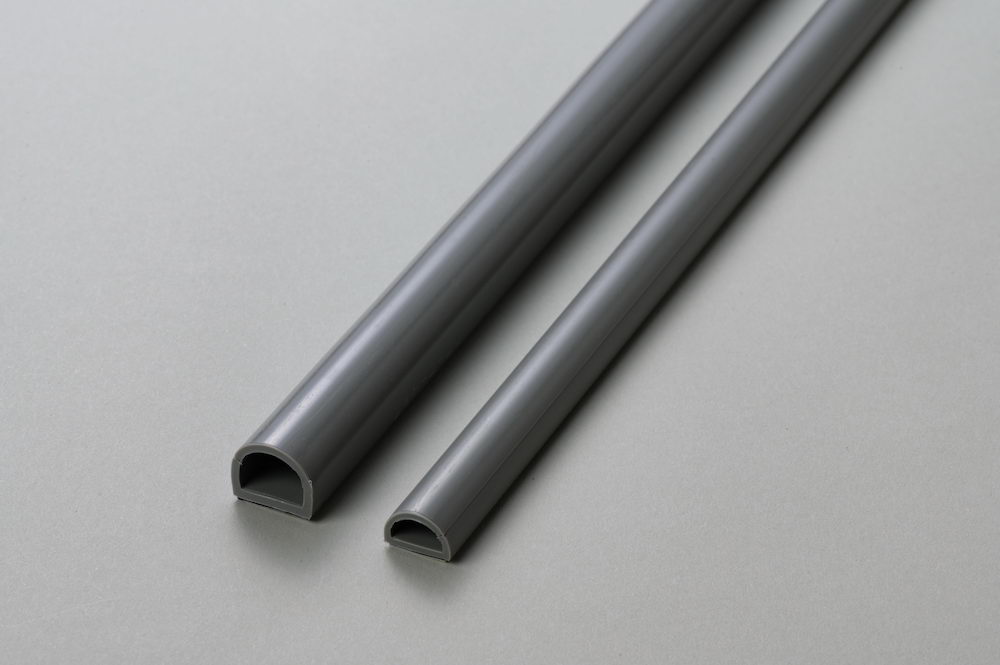
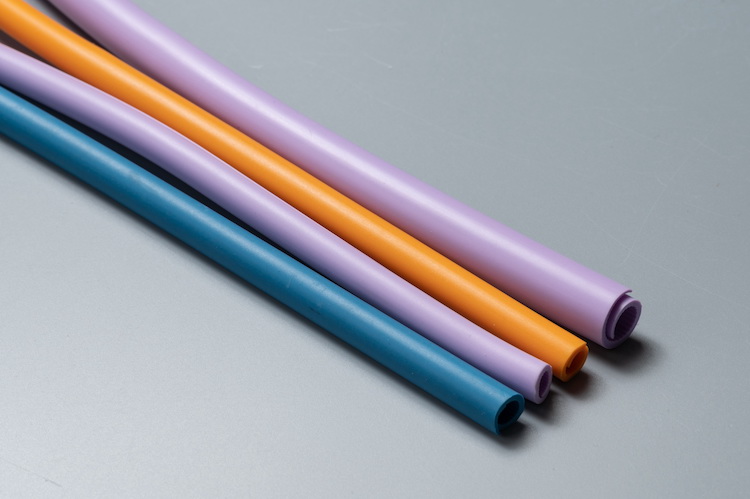
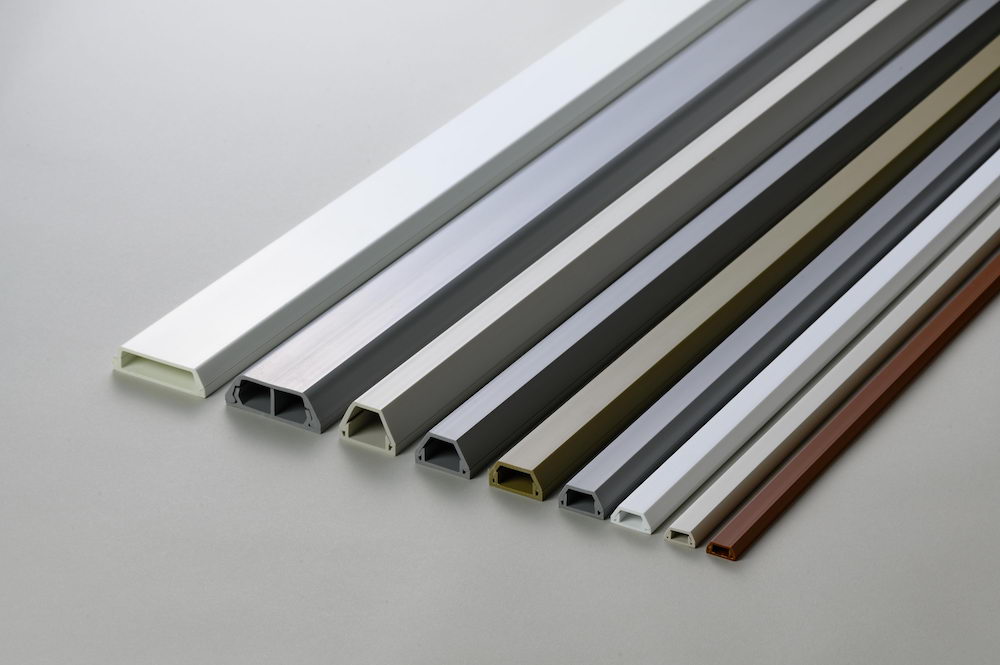